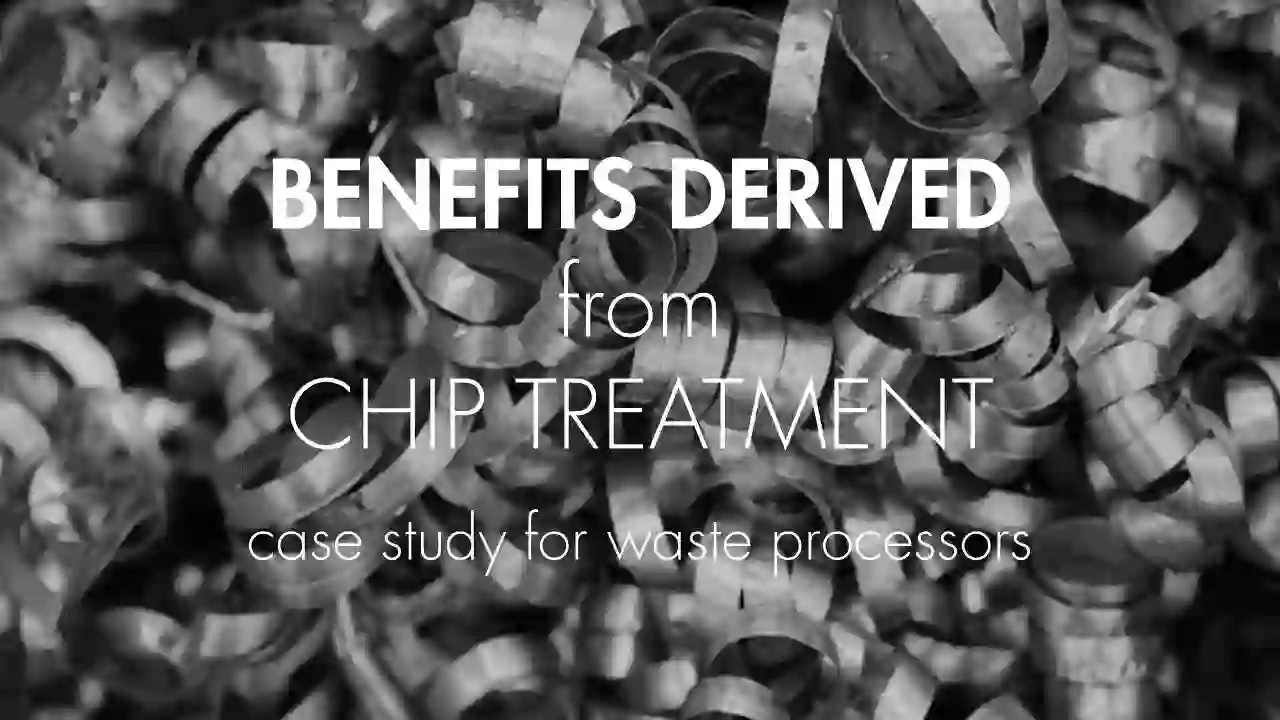
BENEFITS DERIVED FROM THE CHIP TREATMENT FOR WASTE PROCESSORS
The chips generated during machining processes are impregnated with oils or emulsions, a state in which it is impossible to recover the material without prior separation of the fluids.
Thanks to the separation of the material from the fluids, we are able to recover the chips and, therefore, value them. This process is carried out in five different phases:
- Screening
- Shredding
- Centrifuging
- Magnetic separation
- Filtering
If the short chips and the long or skein-shaped chips coexist, it is recommended to previously place a sieve for their classification.
Thus, the short chip can go directly to the centrifuge, and the skein-shaped swarf is directed to the crusher so that once crushed, it returns to the centrifuge and so achieves the completion of the complete treatment process.
The objective of shredding the material is to obtain chips with a short and optimal geometry for the subsequent centrifugation process.
From here, the continuous centrifugation process can begin, in which, on the one hand, it is possible to reduce the degree of humidity of the chips by 97% and, on the other, we recover the oil or emulsion that has been used in the manufacturing or machining process.
"Cometel Recycling Solutions ' chip treatment systems convert metal waste and cutting fluids into a source of income for your company".
Depending on the material and the type of refrigerant used, humidity levels below 0.8% can be reached after centrifugation.
Obtaining a degree of humidity lower than the primary allows, after the centrifugation process, a much more efficient separation between ferrous and non-ferrous materials, since the magnetic force will not be diminished by the humidity of the materials that condition its weight and its adherence.
The filters are located in the last stage of the process to purify the liquid for its later reuse, separating the small solid particles from the refrigerant liquid.
The waste processor has to prepare the chips, separating them from the remains of other metals and materials by various methods. The correct classification of chip types is essential to be able to give the best possible output. And it is that the most valued will always be the purest material, therefore, the purer the material, the greater its value.
We can find 2 situations:
- If you install the line at source (industrial customer facilities), you would avoid hazardous waste license and, also, if the swarf is in a skein/tangle, the savings due to logistics and space costs would increase.
The contract with the client would be secured for a certain period of time, being able to even negotiate the price of the chip, since, thanks to the installation, the client would be recovering soluble/cutting oils, being these reusable materials. - In case of installing the chip treatment line in your plant, you could acquire the chips from different industrial clients. With them crushed, centrifuged, separated and briquetted, the sale amount of the material would increase considerably.
It would report a lower logistics cost, greater manageability, and would avoid price drops by foundries/refineries due to wet chips. At the same time, avoiding all the administrative procedures corresponding to hazardous waste, and their economic penalties.
Consequently, you could sell to each foundry a required alloy, specializing the material and being able to sell the product at a higher price.